Robots don’t replace people. They relieve them.
Photo: Bizerba interactive
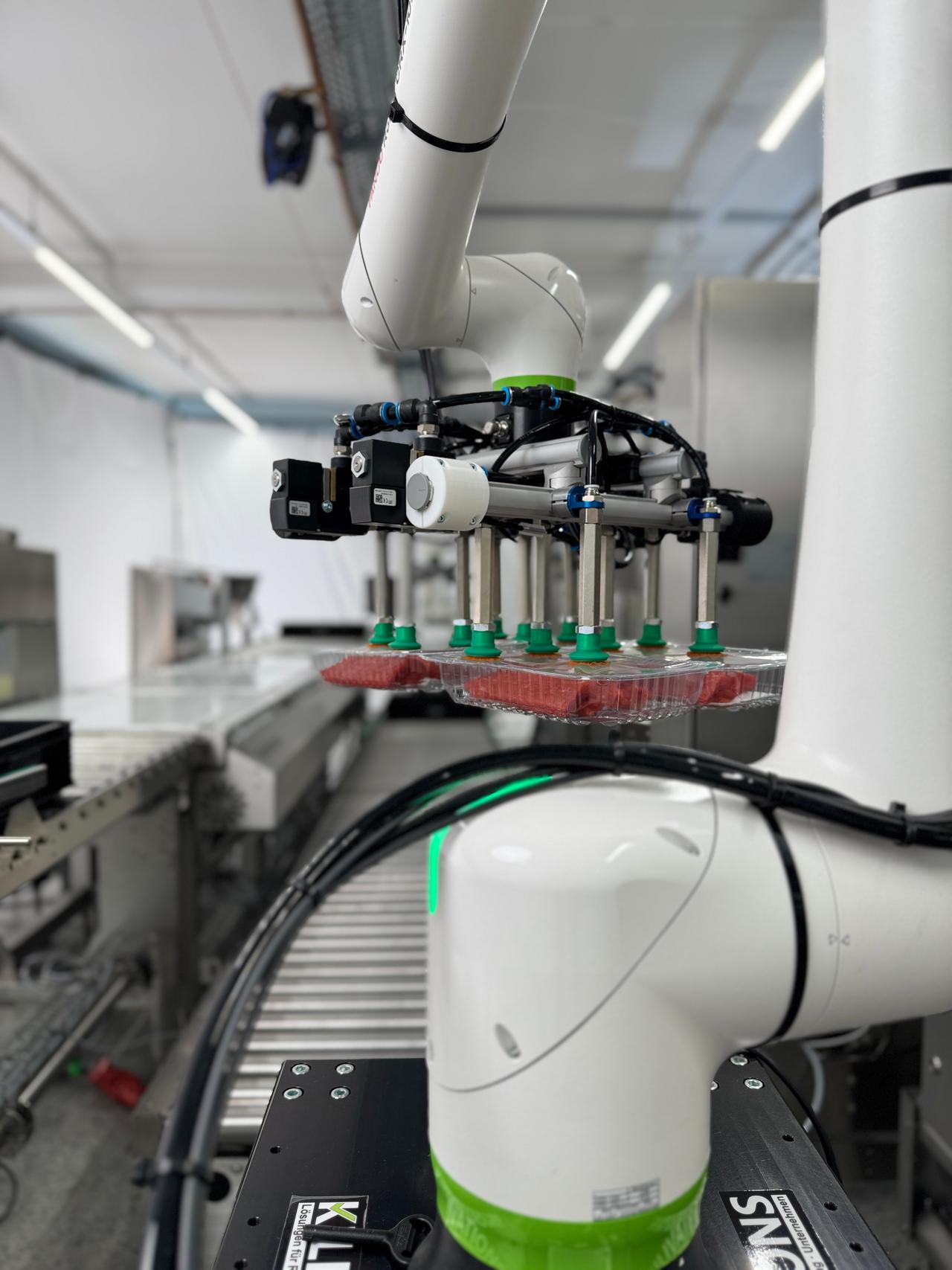
The biggest pressure point for food producers is undoubtedly at the end of the production line. Products need to be labeled, inspected, sorted, packed and palletised, but in many places there simply aren’t enough skilled workers to carry out these tasks reliably, shift after shift. At the same time, demands for quality, traceability and hygiene are increasing. This combination means that automation in the end-of-line process is an absolute necessity, not just a nice-to-have.
It's a common misconception. It's not about replacement. It's about providing relief. Robots take over simple, repetitive or physically demanding tasks. For example, aligning and loading products into boxes. This frees up staff capacity elsewhere and ensures consistent quality, even at high throughput. Robots don’t replace people. They relieve them.
Mainly repetitive ones. Examples include sorting, aligning, grouping, loading and palletising. Labeling and inspection also offer great potential, and this is an area in which we can deliver top precision. However, the real power lies in combination. This is a well-designed, integrated solution where all modules work seamlessly together and fit into existing production environments.
It depends on the situation. In practice, however, we have seen labour savings of up to 40 per cent in packaging areas. This doesn't mean that people are being replaced. It means we can fill staffing gaps, stabilise processes and increase output, which clearly benefits the business.
That’s a valid concern. That’s why we use scalable modules and open interfaces, and we work closely with our technology partners. Our systems can be integrated into existing lines with minimal disruption. What's more, our BRAIN2 software provides the transparency and traceability that modern operations require. This makes automation not only efficient, but also audit-proof.
Don't wait until the pressure becomes unmanageable. Even small steps towards automation can provide significant relief. The key is to partner with someone who understands production realities and recognises that automation is a tool for achieving better quality, faster throughput and greater resilience, not an end in itself. That’s exactly what we offer at Bizerba.
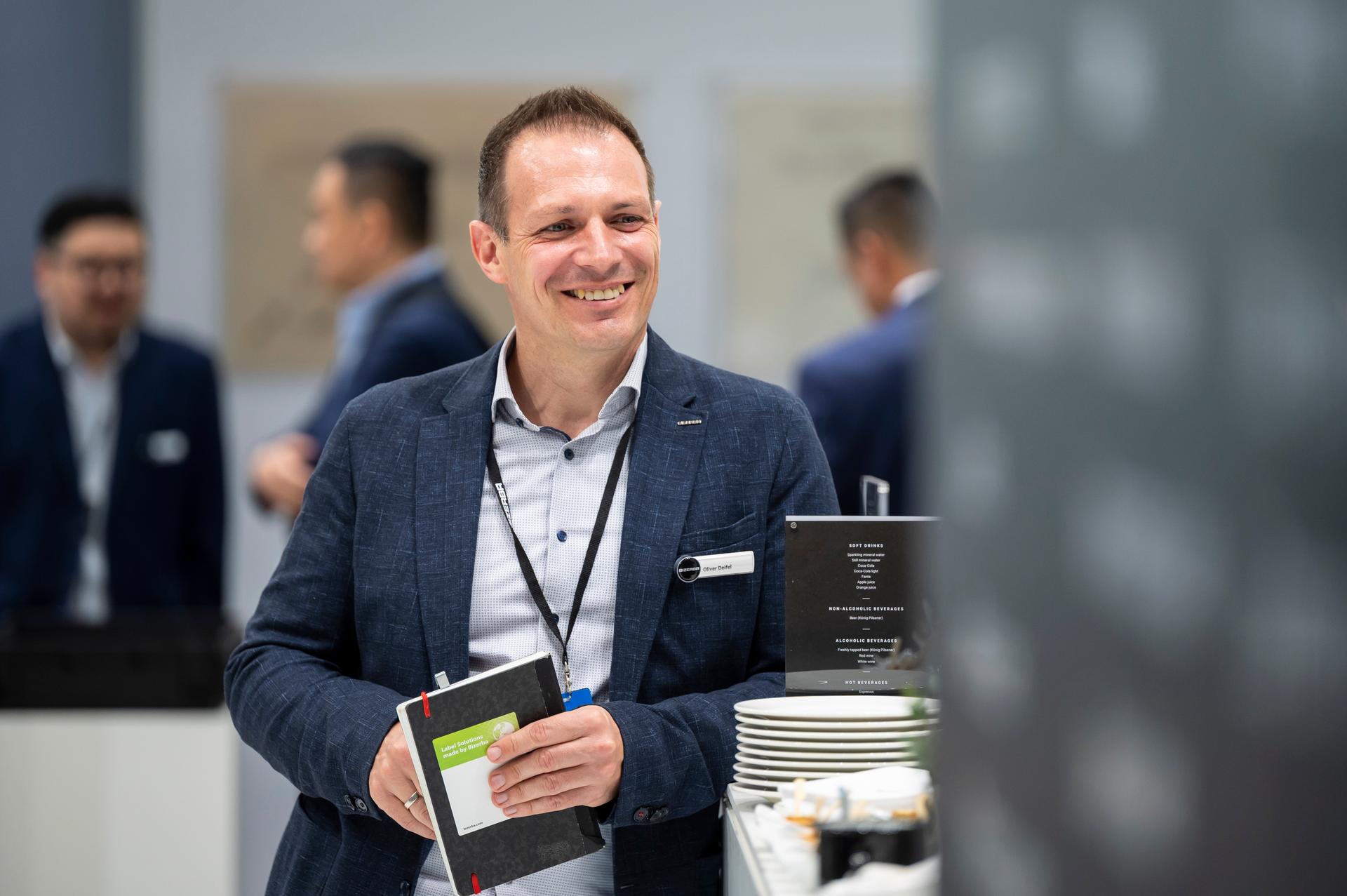
Bizerba SE & Co.KG
Want to know more?
Your message is on it’s way
The form was sent successfully
Oops, something went wrong here
An error occurred when sending the form. Please try again