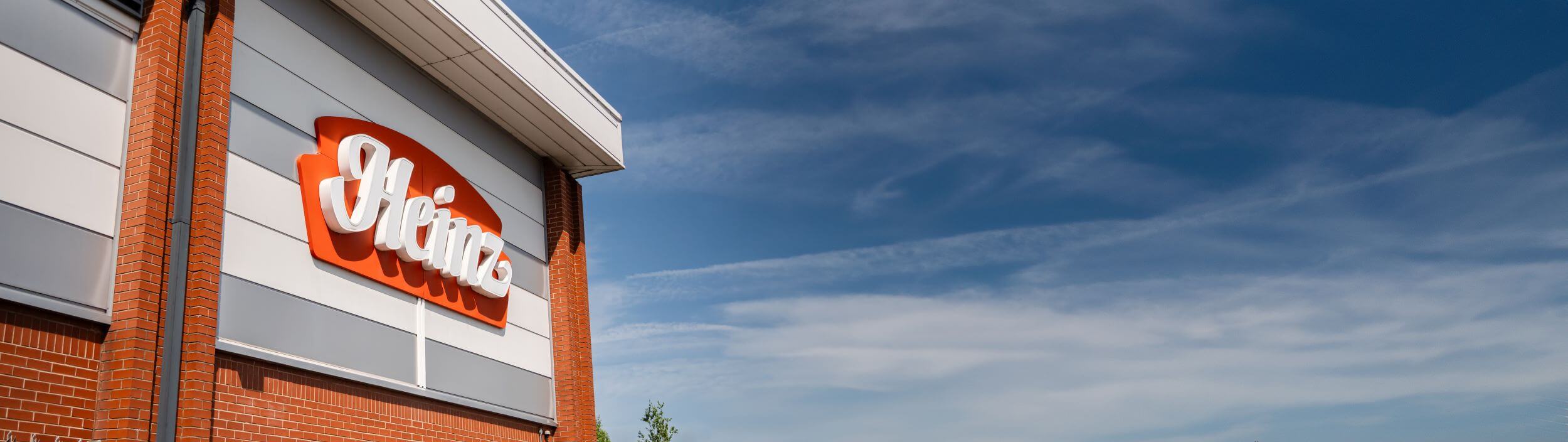
- Année de création : 2015 (fusion)
- Siège social : Chicago, IL / Pittsburgh, PA, USA
- Présence mondiale : présent dans plus de 40 pays avec 75 usines dans le monde
- Spécialité du produit : aliments et boissons de qualité pour les consommateurs et les entreprises du secteur de la restauration.

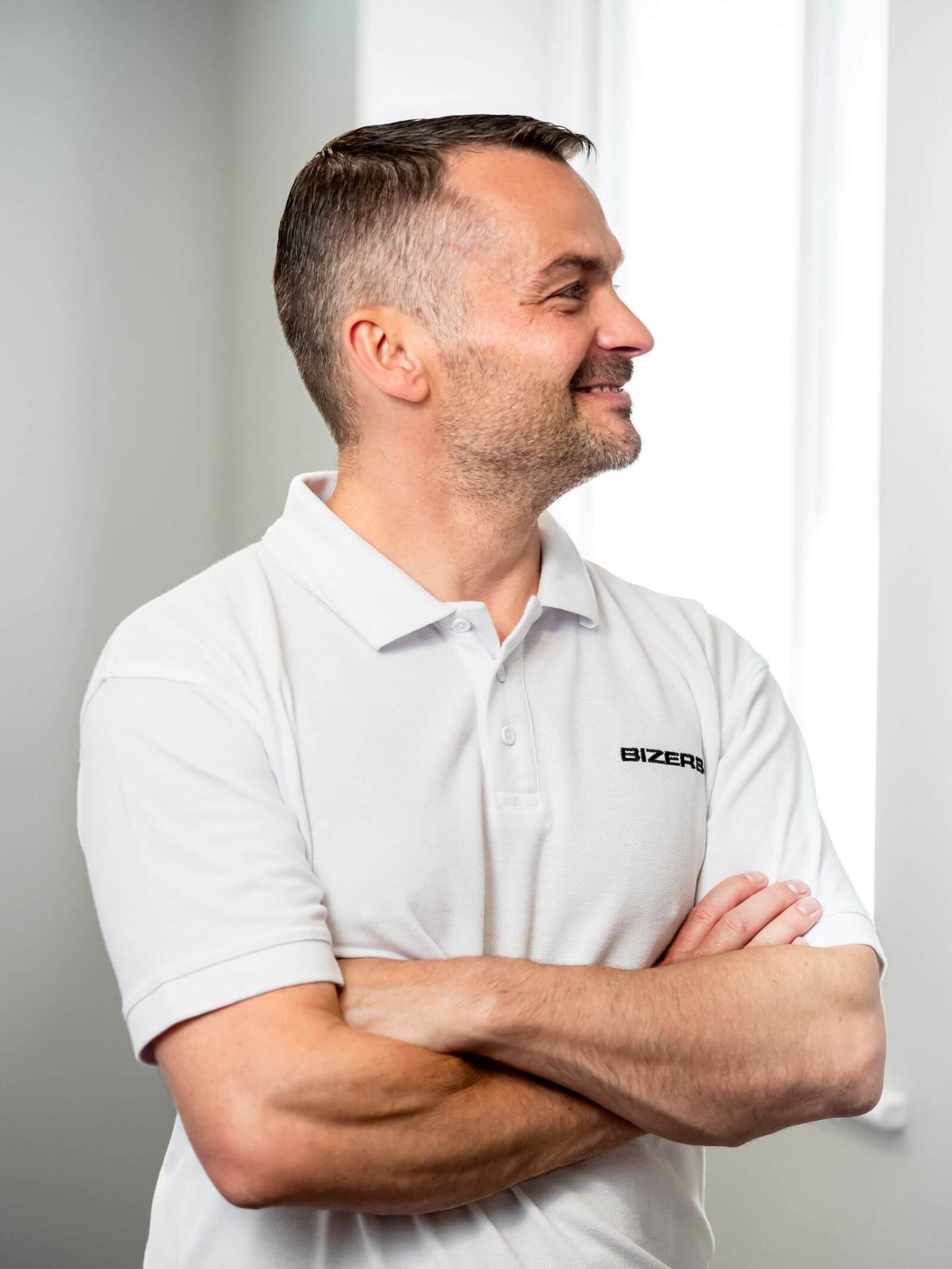
Coûts et temps d'arrêt évitables
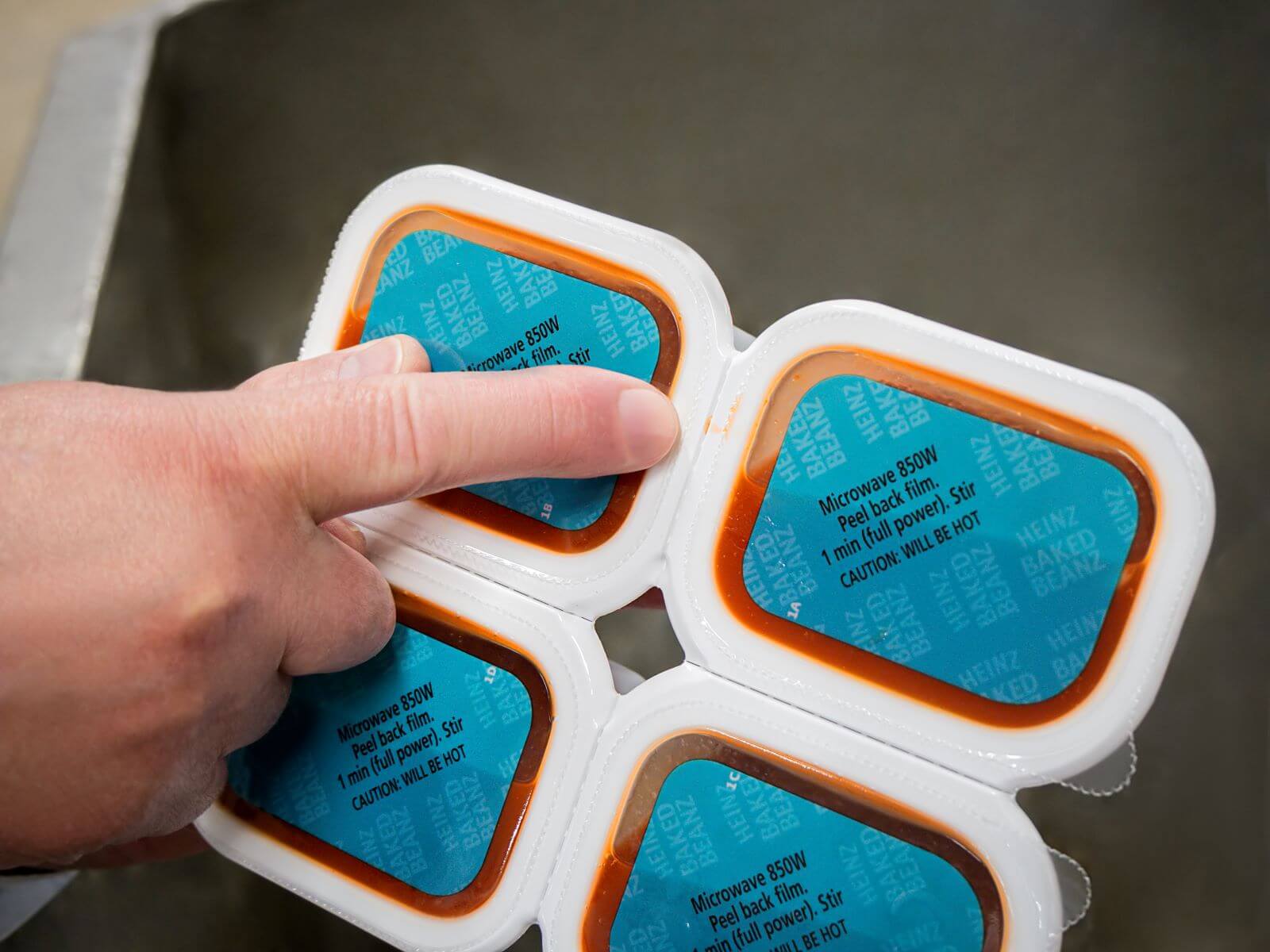
Le système d'inspection précédent entraînait des temps d'arrêt évitables et une augmentation des coûts de production. Des dépenses de réapprovisionnement en eau aux coûts unitaires plus élevés menaient à davantage de temps d'arrêt. Il était clairement temps de changer, a décidé Lee Reece, responsable mondial de l'excellence technique FSQ chez Kraft Heinz.
Se concentrer sur les nouvelles technologies
"Le pot peut se détériorer de différentes manières. Qu'il s'agisse de sauce piégée dans le cordon de soudure, de surchauffe du scellage ou d’une pression inadéquate pour garantir l’étanchéité. Nous avions besoin d'un système capable de détecter toutes ces défaillances", explique M. Lee.
Des enjeux importants, des attentes claires
L'équipe de Kraft Heinz recherchait un système capable d'améliorer l'efficacité globale de l'équipement. Mais aussi de minimiser les risques opérationnels et de garantir l'étanchéité du produit. Pour ce faire, il fallait détecter les moindres anomalies : des cloques de plus de 2,5 mm, des dépôts de sauce ou de haricots dans la zone de soudure, des ruptures de soudure ou des films froissés. Les attentes étaient très claires.
Système d'inspection par vision sur mesure
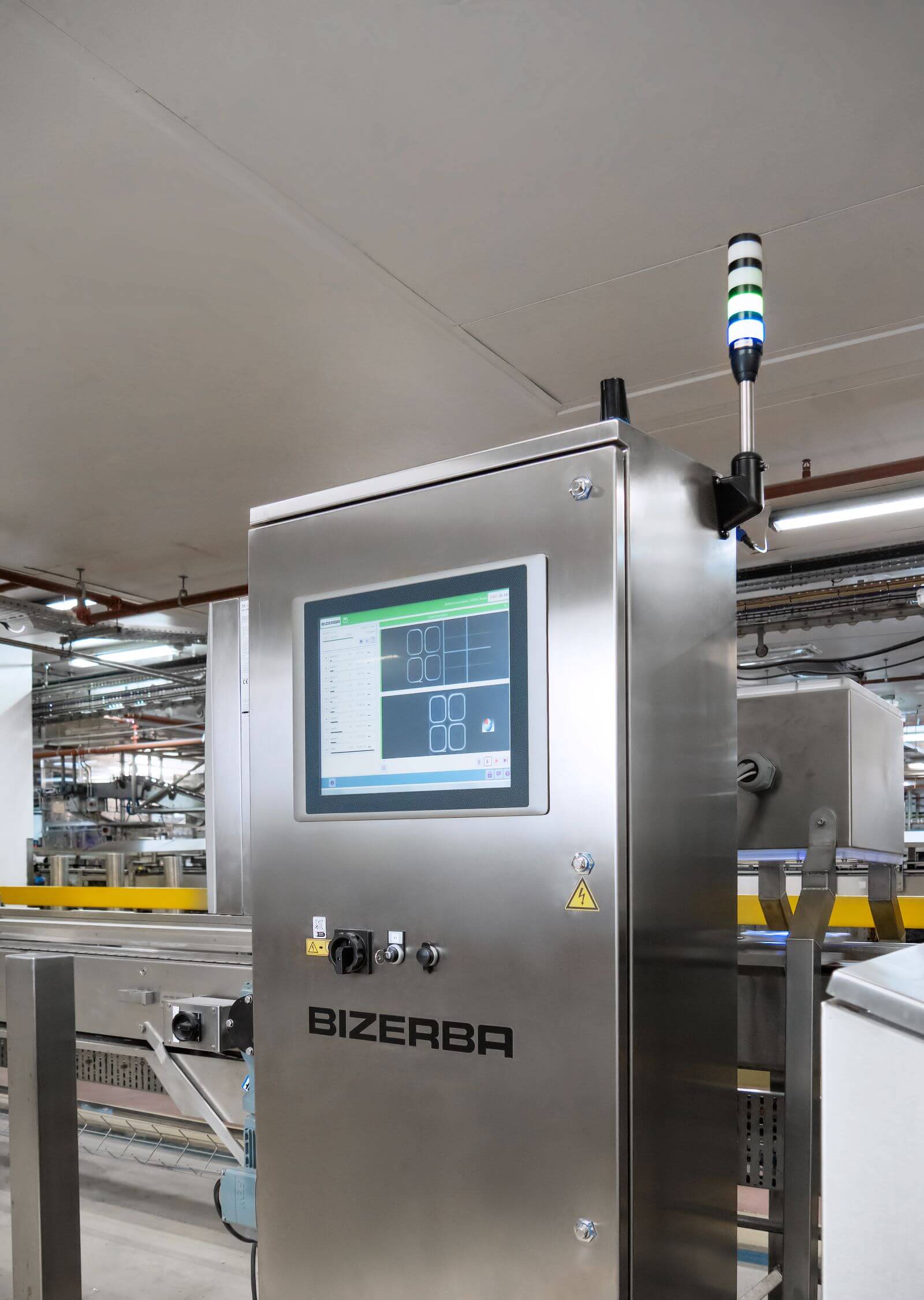
Bizerba a proposé un système d'inspection par vision entièrement personnalisé, conçu spécifiquement pour les besoins de Kraft Heinz, sans perturber la production existante. Le cœur de la solution : le SealSecure enrichi du logiciel industriel BRAIN2 de Bizerba et du module logiciel BRAIN2 Capture pour une documentation et une traçabilité sans faille.
Point clé : la simplicité de la mise en œuvre
Pour garantir une mise en œuvre rapide et économique, l’équipe de Bizerba a adapté la solution à l’infrastructure existante de Kraft Heinz. Elle a intégré le système sans modifier le convoyeur ni le dispositif d'éjection.
"Cela signifie que nous avons adapté notre système à la ligne de Kraft Heinz, et non l'inverse", explique Adrian Allcroft, Directeur technique des ventes - Nord-Est, Bizerba UK Ltd.
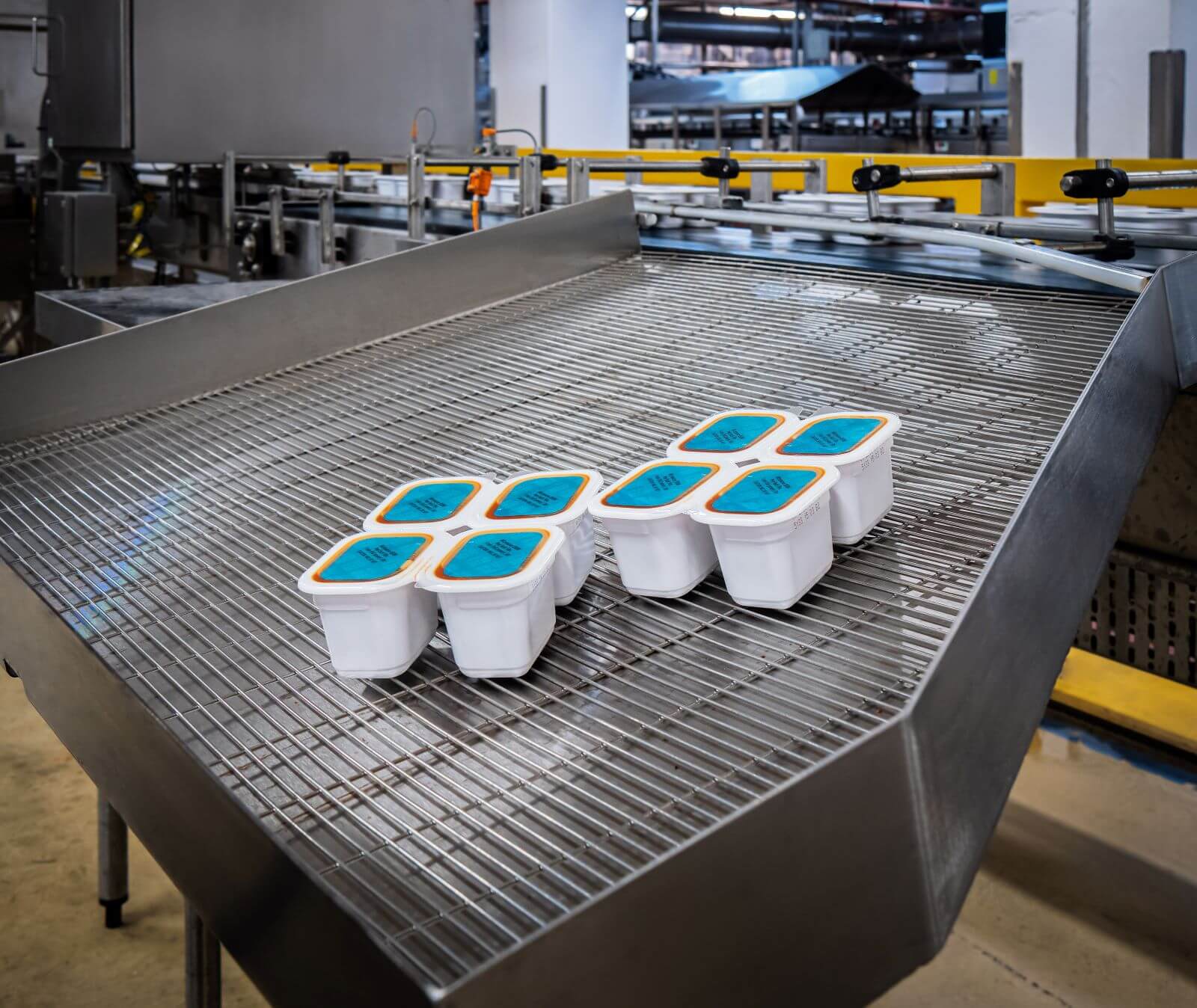
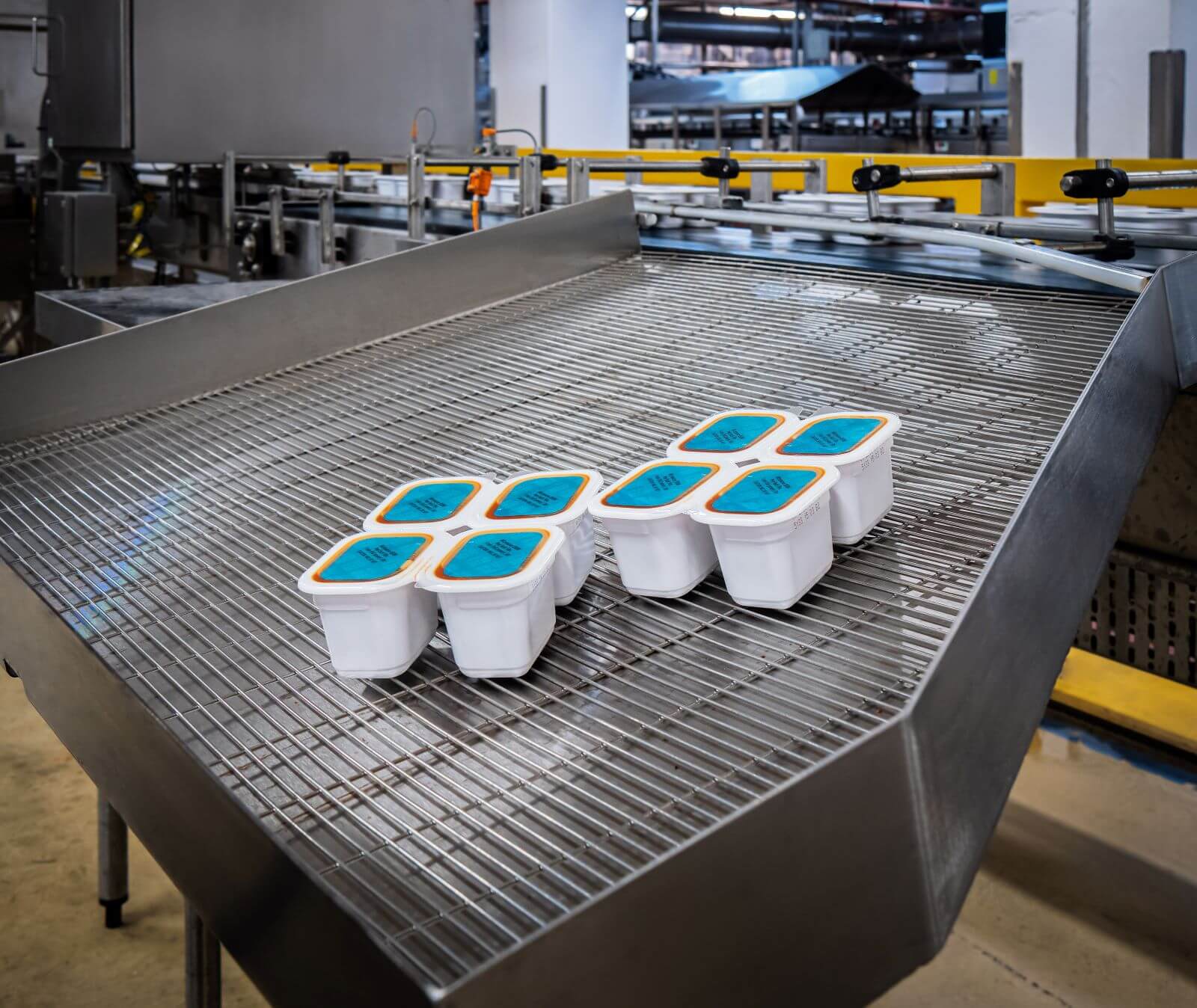
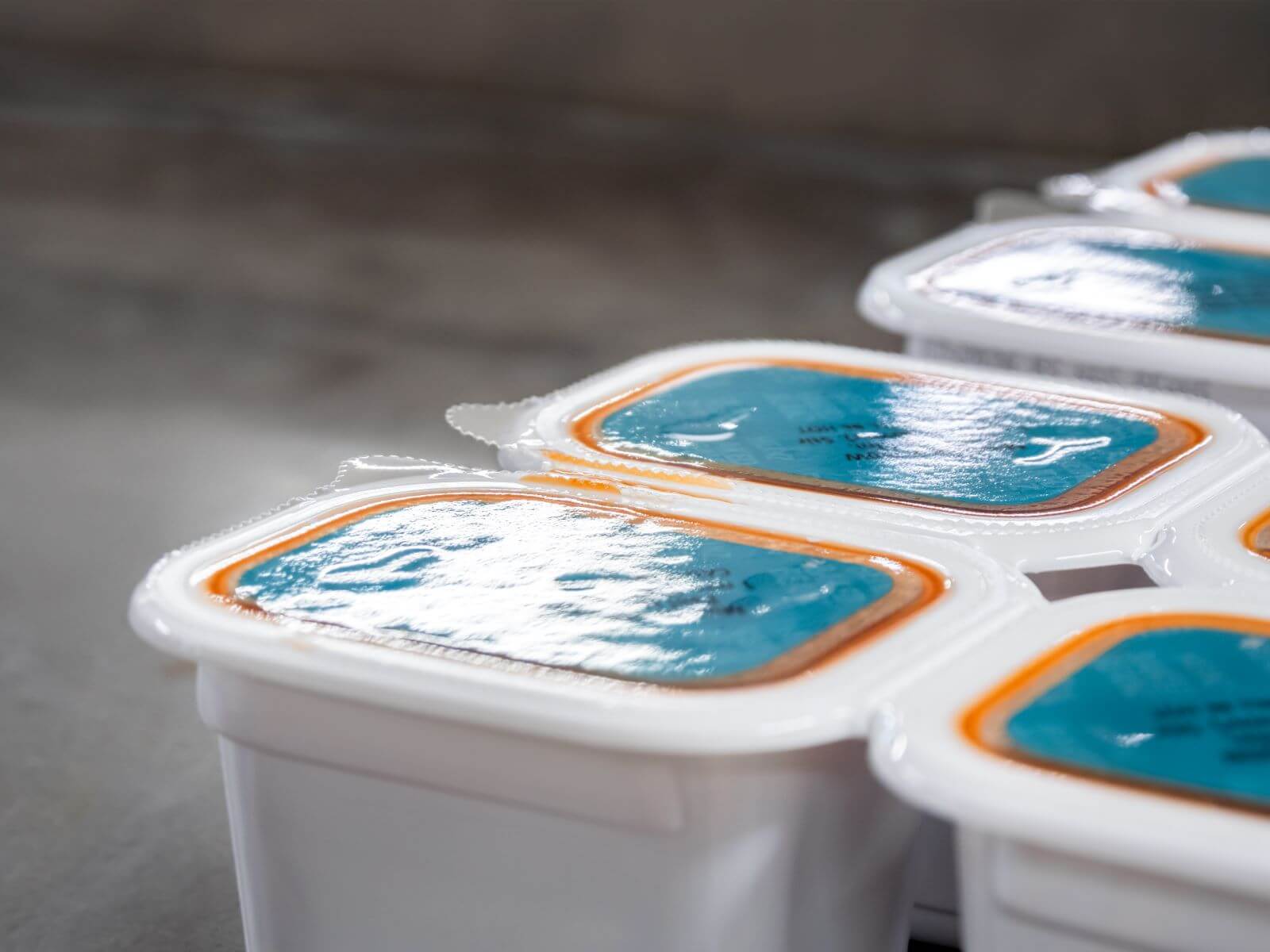
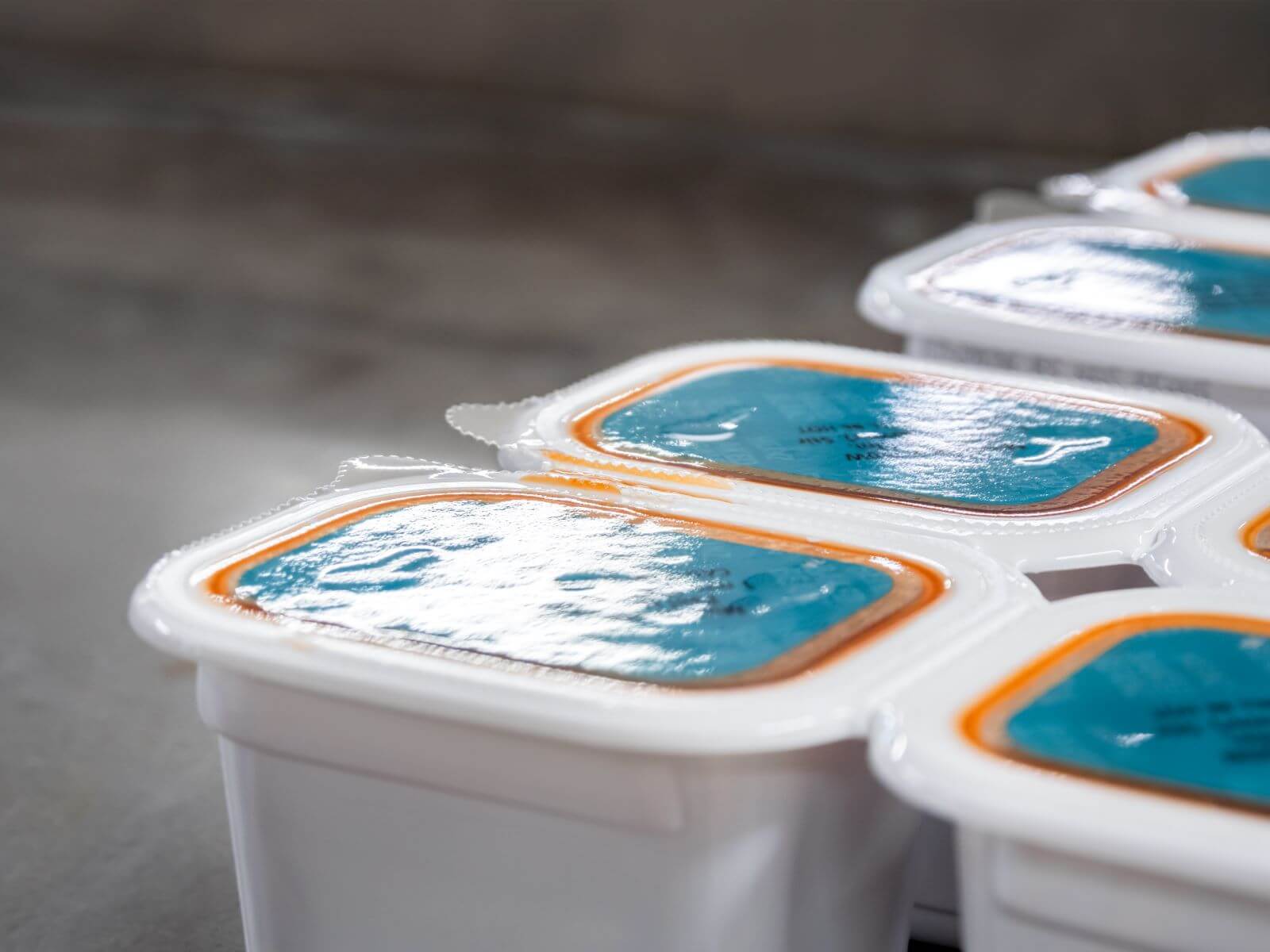
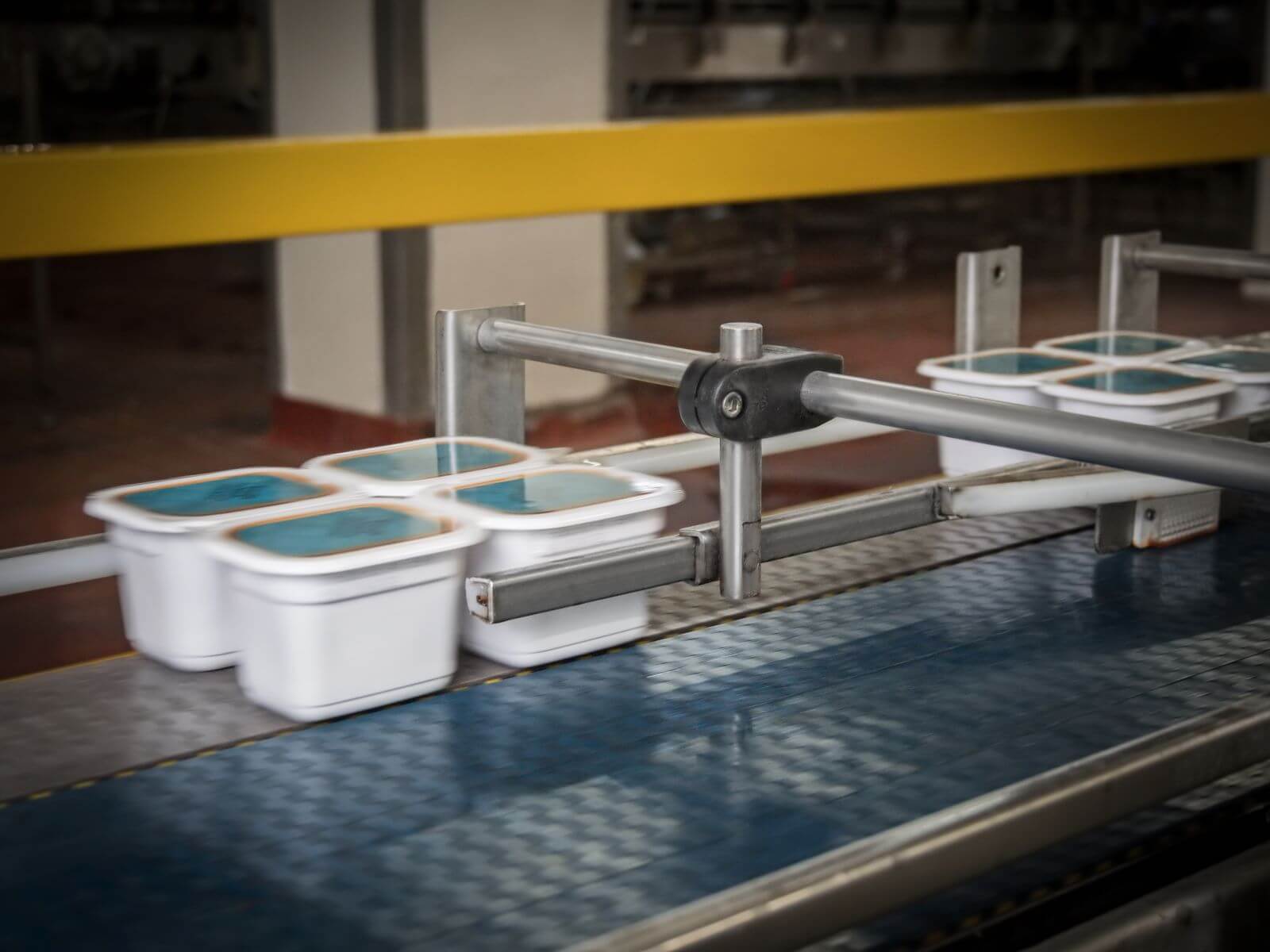
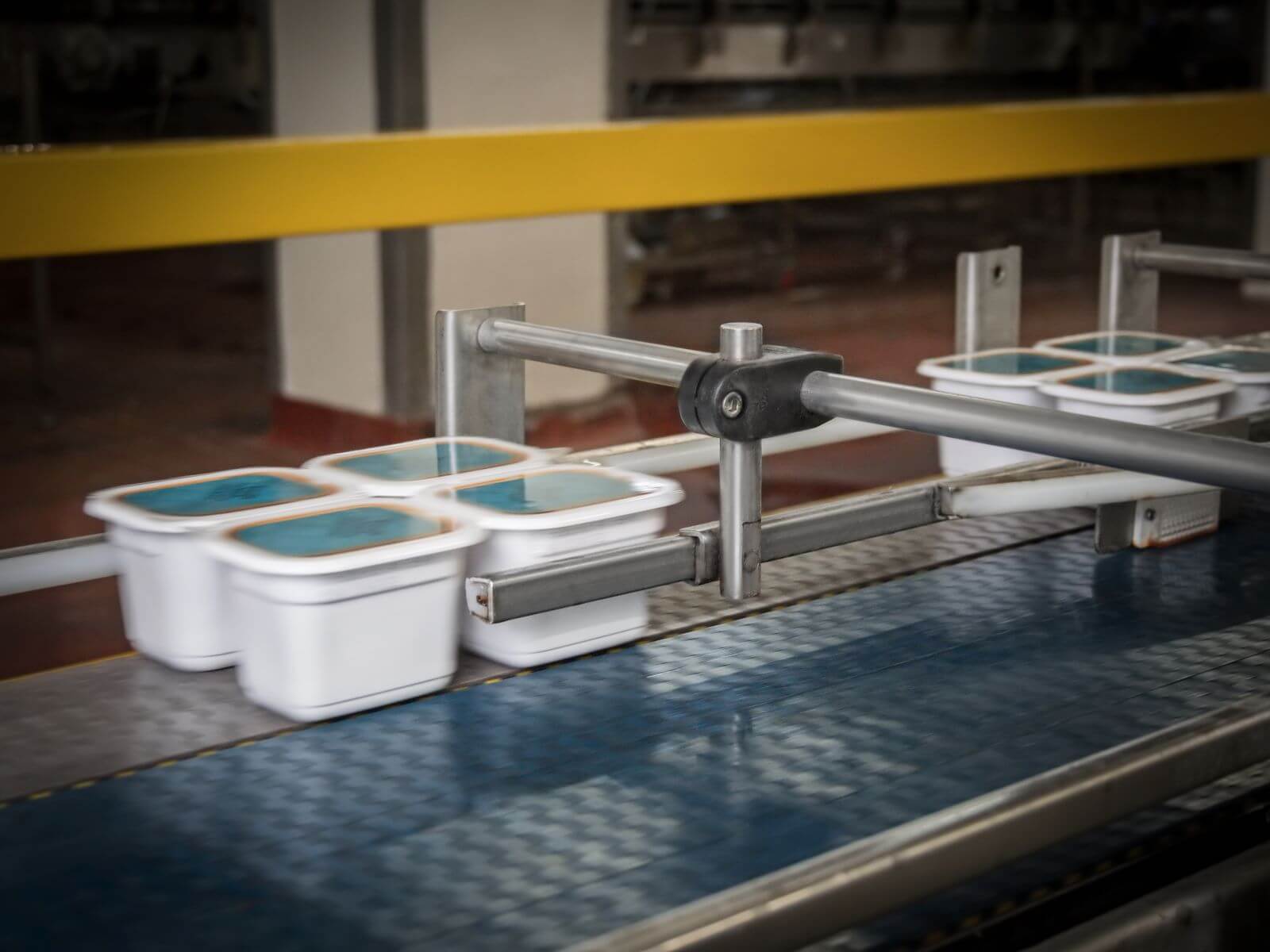
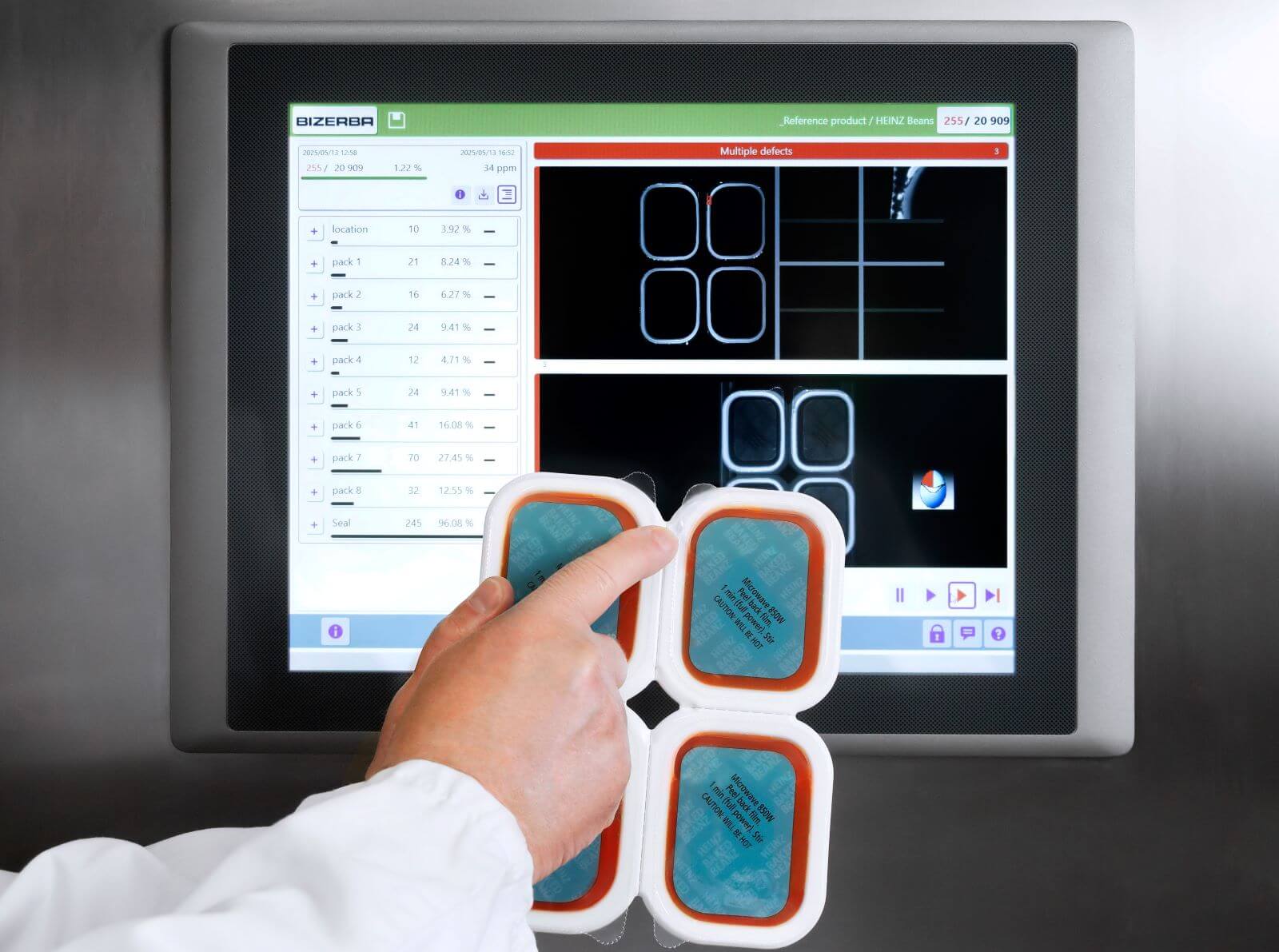
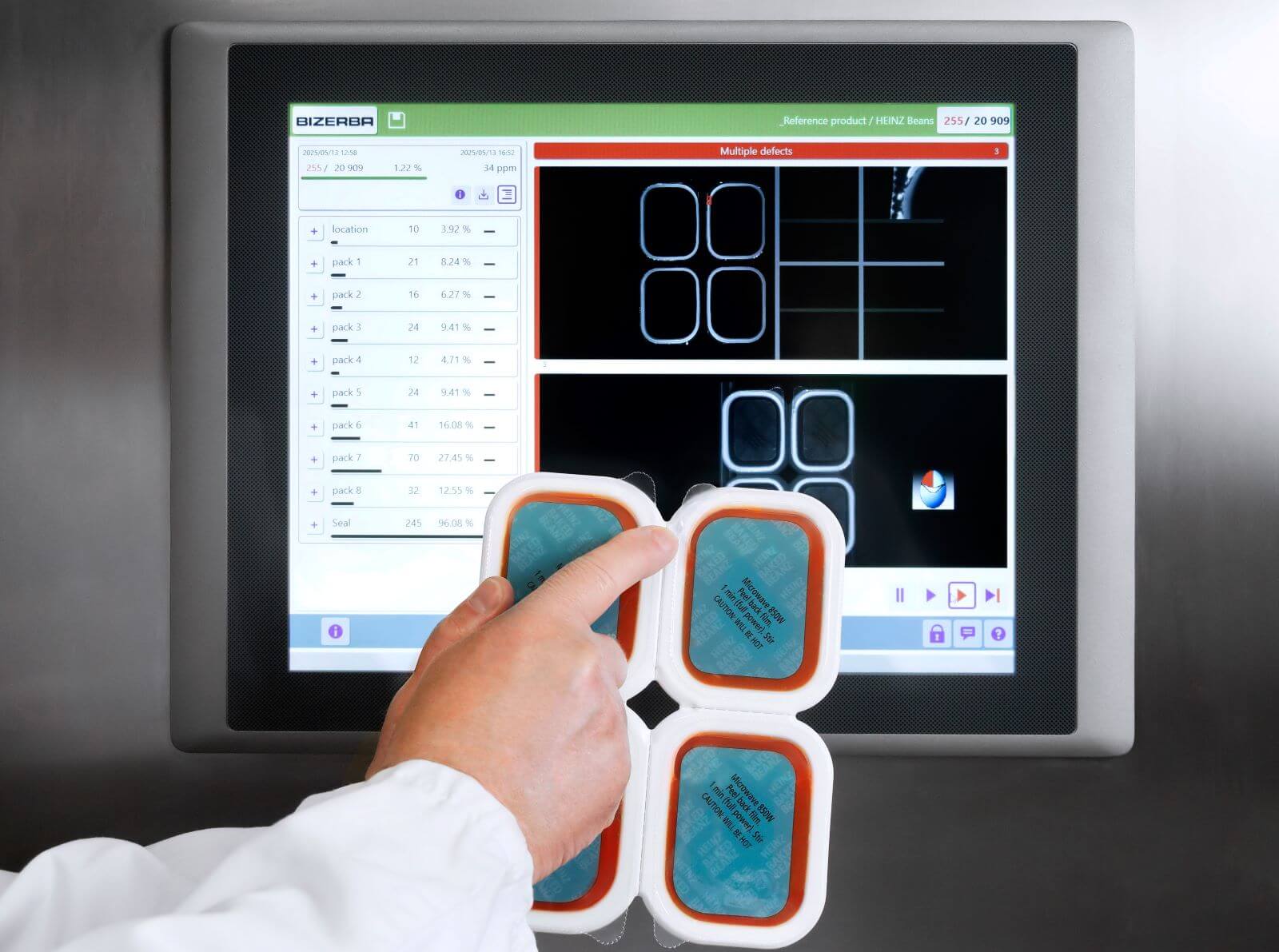
Intégrité et efficacité des joints
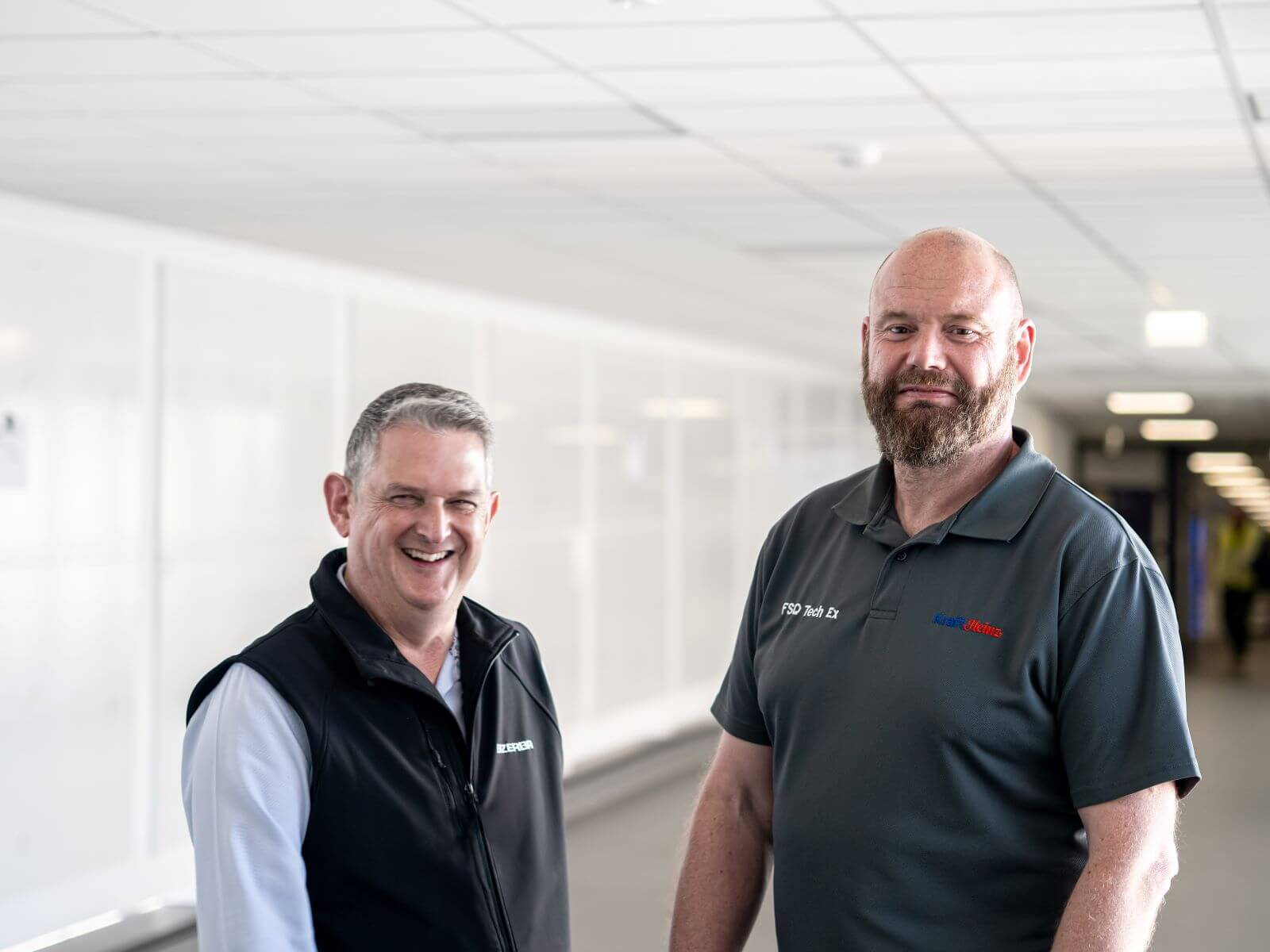
La nouvelle solution répond aux normes de scellage rigoureuses de Kraft Heinz. Il n'y a pas de résidu de sauce ou de haricot dans la zone de scellage, pas de rupture de scellage, pas de film froissé et pas de cloques de 2,5 mm ou plus.
Après six semaines, les résultats parlent d'eux-mêmes : une plus grande confiance dans l'intégrité du scellage, moins de problèmes de qualité et un flux de production plus fluide. Les opérateurs ont loué la facilité d'utilisation du système. L'équipe de Kraft Heinz voit un potentiel à long terme dans sa capacité à réduire les temps d'arrêt, prévenir les réclamations et protéger l'intégrité de la marque.
La qualité de l'assistance a été l'un des facteurs déterminants de la réussite du projet
"L'impact a été significatif. Nous avons constaté une amélioration de l'efficacité de la ligne. Nous avons empêché les défauts de scellage de se propager plus loin dans le processus", déclare Lee Reece.
Il ajoute : "L'assistance que nous avons reçu dès le début a été l'un des facteurs déterminants de la réussite du projet. Ce fut un plaisir de travailler avec Bizerba".
Pour l'avenir, il ajoute que l'esprit d'innovation de Bizerba et sa capacité à fournir des solutions personnalisées et intégrées au logiciel en font un partenaire technologique précieux à long terme : "C'est un partenariat qui se développe chaque jour", confirme Adrian Allcroft.
Comptons
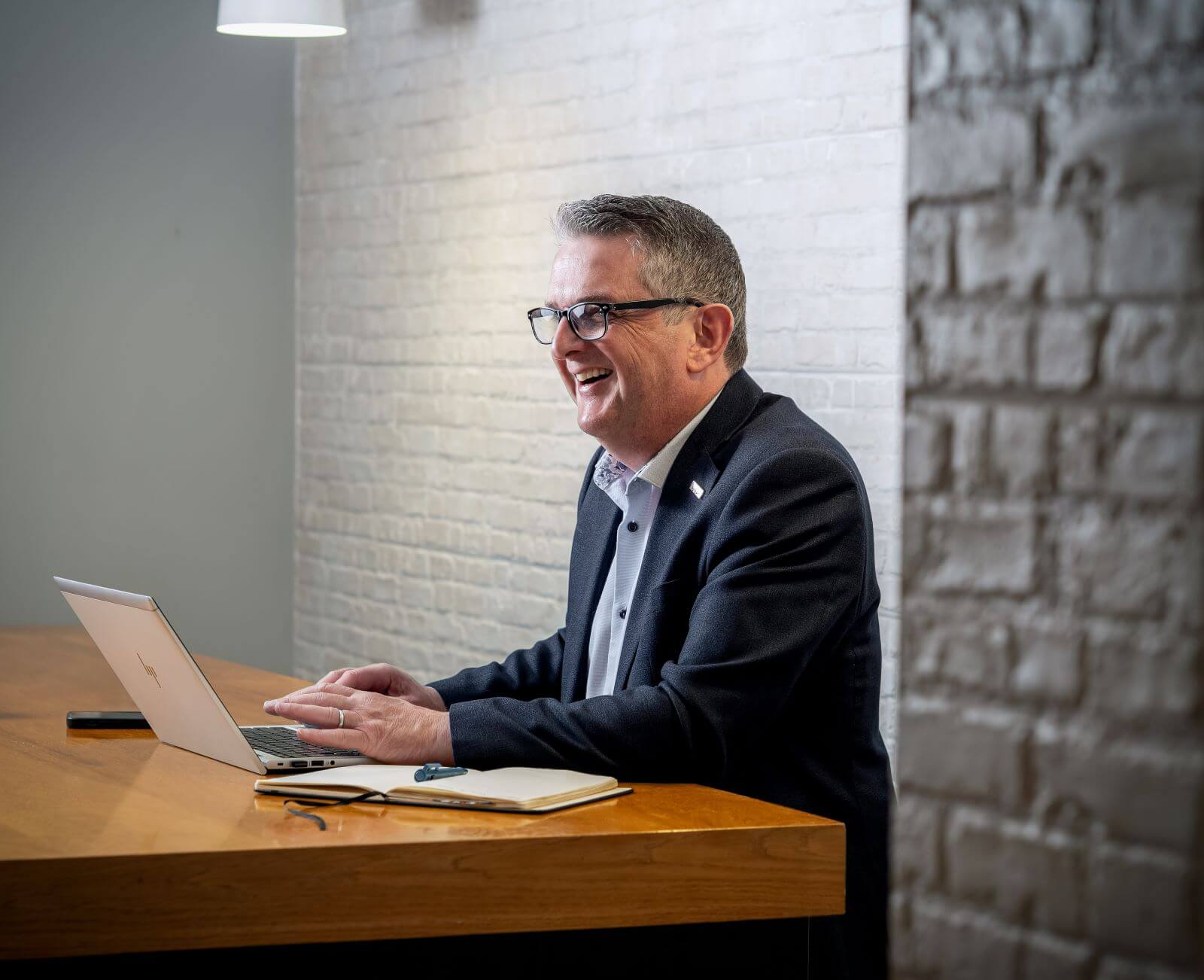
La solution Kraft Heinz Wigan
Téléchargements
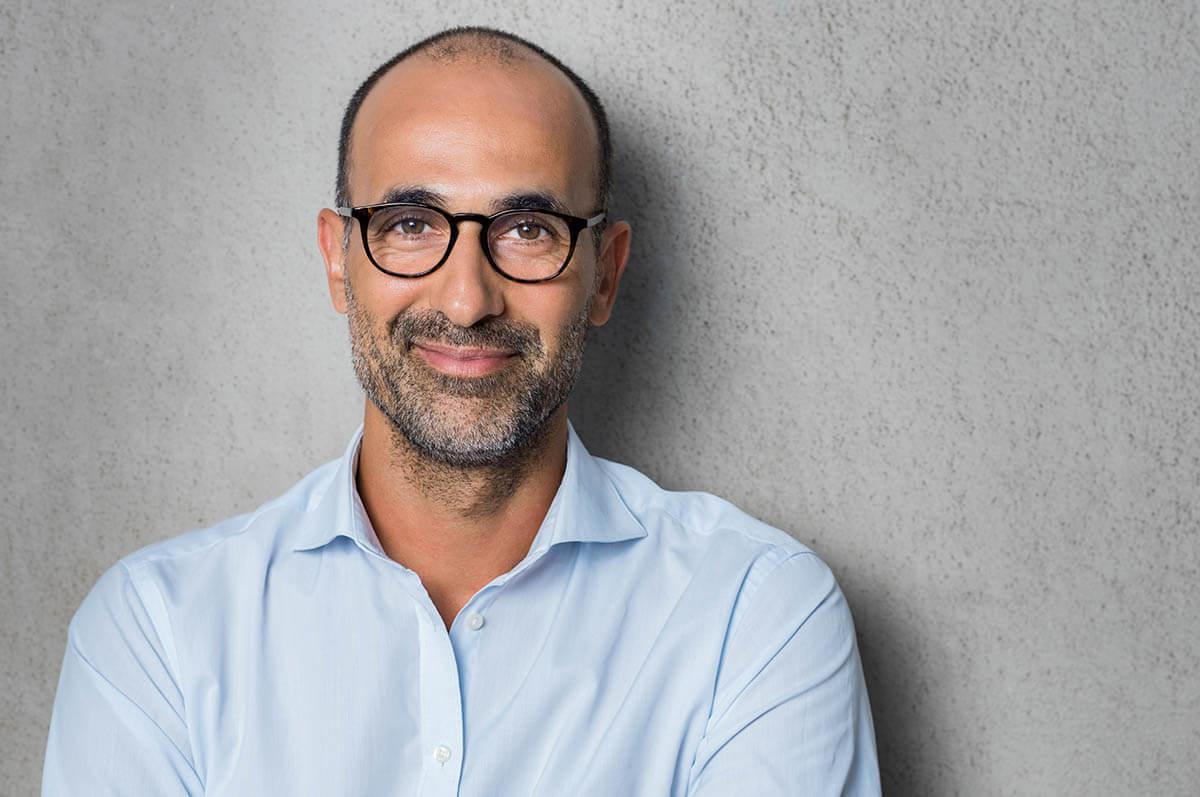
Votre message a bien été envoyé
Merci pour votre demande, le formulaire a bien été envoyé
Oups, quelque chose s’est mal passé
Une erreur s’est produite lors de l’envoi du formulaire. Merci de réessayer